AUTOMOTIVE,
DEWETRON simplifies data acquisition across the entire mobility industries with flexible, user-exchangeable modules, isolated inputs, and real-time data processing. Our solutions offer seamless test bench integration, compact mobile or high-channel rackmount hardware, and an intuitive measurement software, making them ideal for testing all types of vehicles—from cars and 2-wheelers to trains, trucks, busses and even excavators. Whatever your testing needs, DEWETRON provides the perfect DAQ solution for passenger or goods transportation vehicles.
E-MOBILITY & Automotive
As electric vehicles are a fixed part of our present and future, DEWETRON is your trusted partner for analyzing, testing, and verifying them. Our automotive testing solutions are ideal for both real drive tests and test benches. With advanced features in our OXYGEN measurement software, designed for electrical power analysis, we offer the perfect equipment for testing, electric, or hybrid engines. Whether you’re working on pure electric or hybrid vehicles, we ensure precise and reliable results.
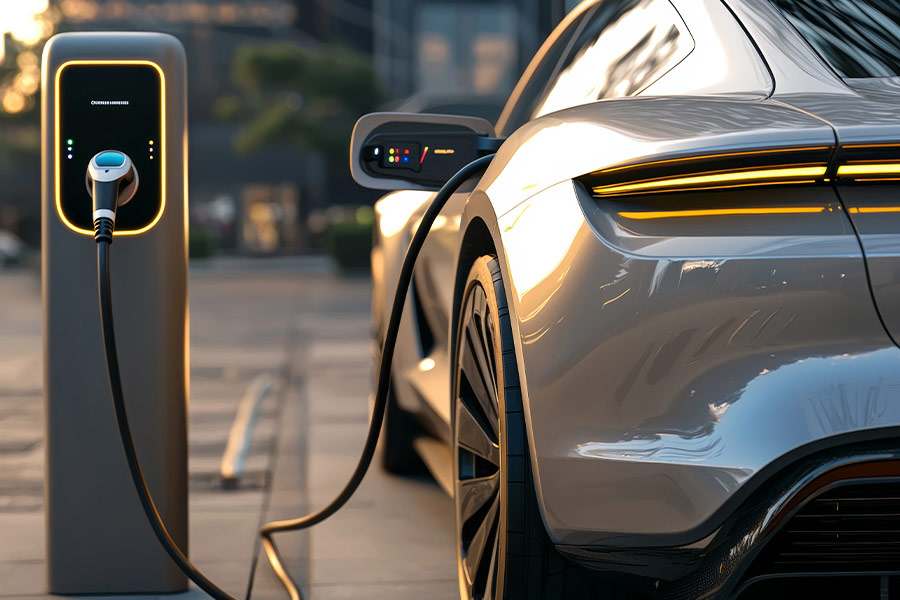
Transportation
DEWETRON DAQ systems are essential for testing and validating rail infrastructure throughout design, production, and operation. Our solutions handle everything from testing electric engines to performing passenger comfort and acoustic NVH tests. Our test and measurement systems play a key role in ensuring the quality and safety of railway power infrastructure, supporting green logistics and high-speed passenger mobility.
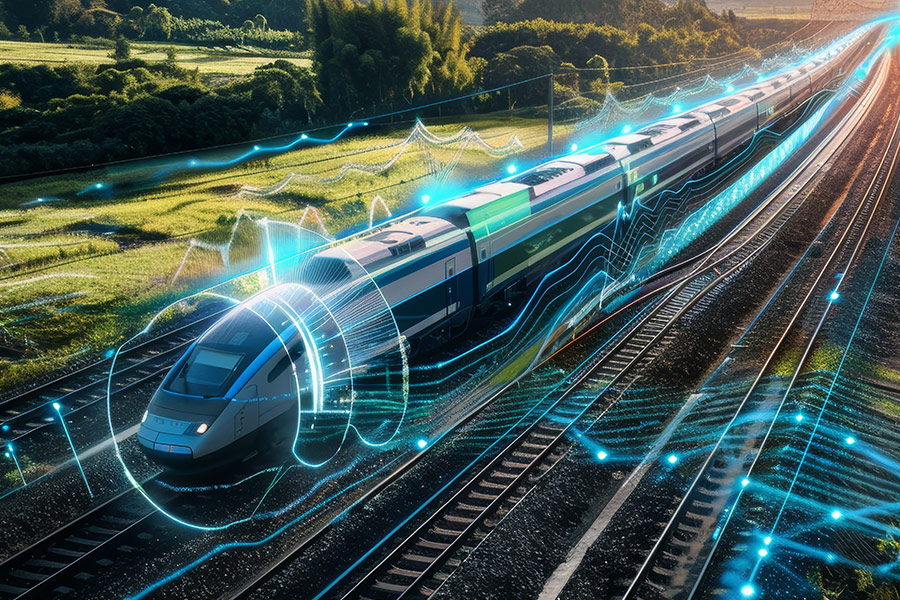
Heavy Machinery
DEWETRON provides the ideal data acquisition solution for testing heavy machinery such as excavators, bulldozers, and other industrial vehicles used in construction, mining, or agriculture. Our test and measurement systems are built to withstand harsh environments, making them perfect for testing electric, hybrid, and alternative powertrains of off-road vehicles and heavy machineries.
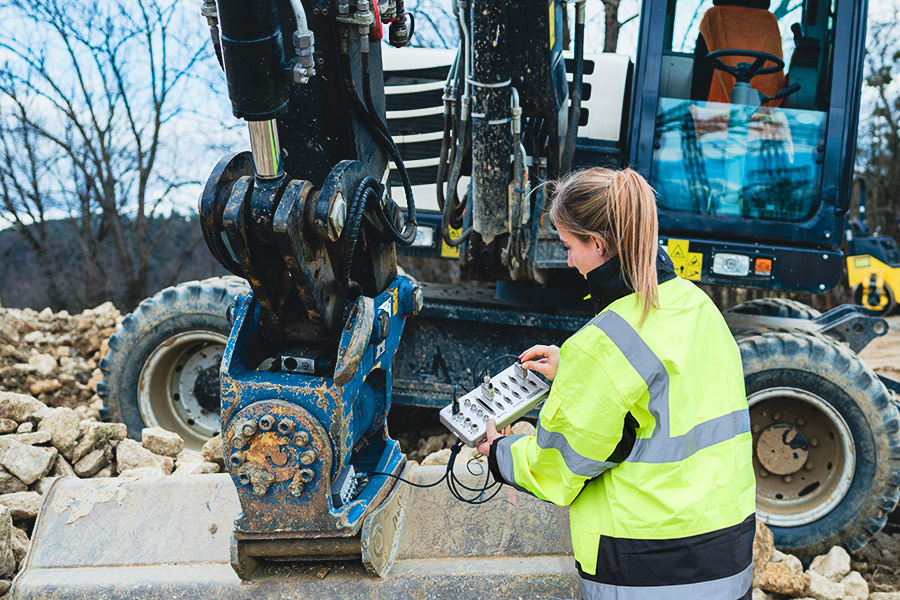